Quality assurance and excellence in logistics are undeniably the pillars of the global flower trade and distribution. These attributes ensure that the delicate flowers ordered by customers worldwide are sourced and transported thousands of miles while preserving their beauty, freshness, and longevity. In East Africa, where some of the world's finest flowers are cultivated, Wafex Kenya has long been recognized as the premier flower sourcing company.
The company has mastered the multifaceted art of delivering floral perfection to customers around the globe. This responsibility falls under Elijah Kabira, the Quality Assurance and Logistics Manager at Wafex Kenya. His vigilant team often orchestrates a careful process encompassing quality checks, ideal packaging, and seamless logistics, which ensures that every flower leaving their facility arrives at its destination in perfect condition, regardless of distance or other challenges.
The Global Reach of Wafex Kenya
Established as a subsidiary of Wafex, Australia's premier flower company, Wafex Kenya has been operational in Kenya for close to twenty years, initially focusing primarily on sourcing and logistics for the Australian market. Under the headship of Claris Wanjohi, the Global Export Manager at Wafex Kenya, the company, however, expanded its business model to cater to the flower needs of the global customer base, growing its services to cover more regions worldwide.
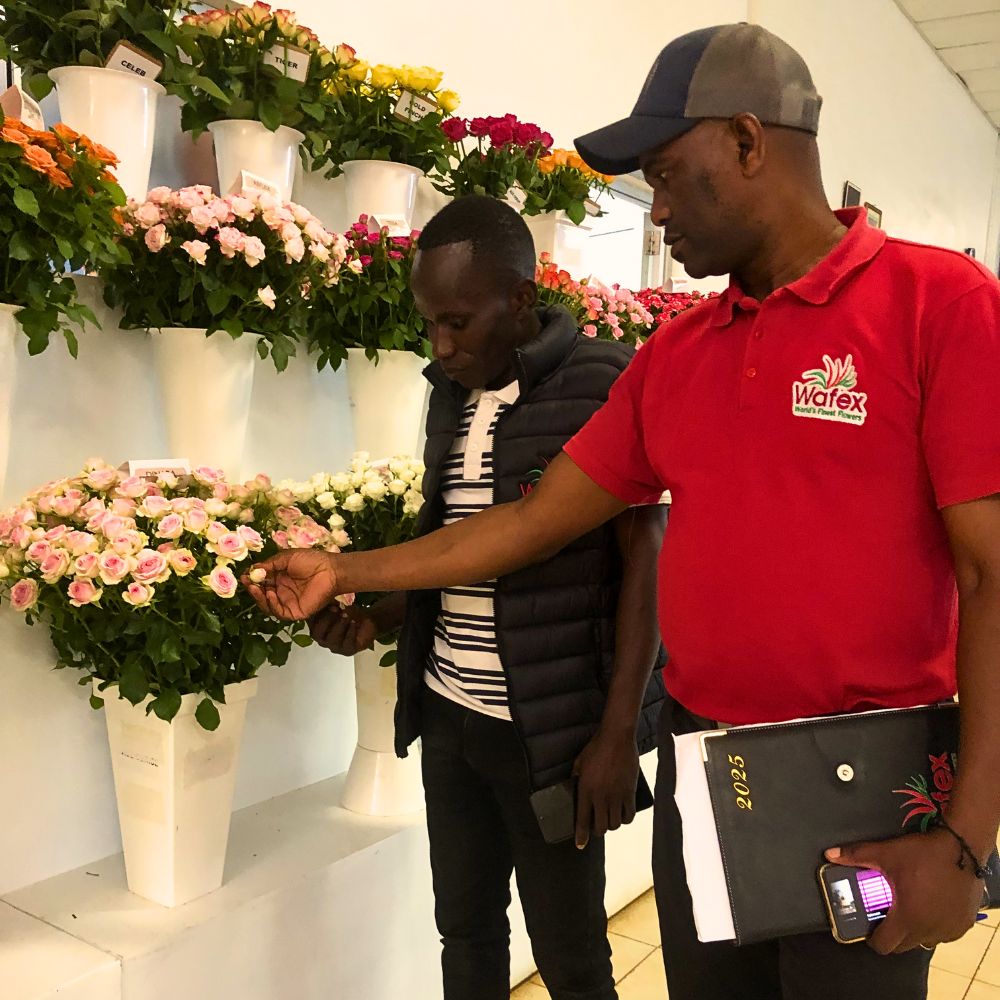
This strategic expansion transformed them into a company with truly global reach, with branches serving clients across Australia, the United States, Kenya, and Ecuador, and a customer base that spans at least 26 countries. The flower sourcing and delivery company's extensive experience in the flower industry, therefore, positions it as a trusted supplier of fresh flowers from Kenya to markets worldwide. Their global network allows them to leverage best practices and adapt and implement cutting-edge techniques in quality assurance and logistics to ensure the highest standards are achieved.
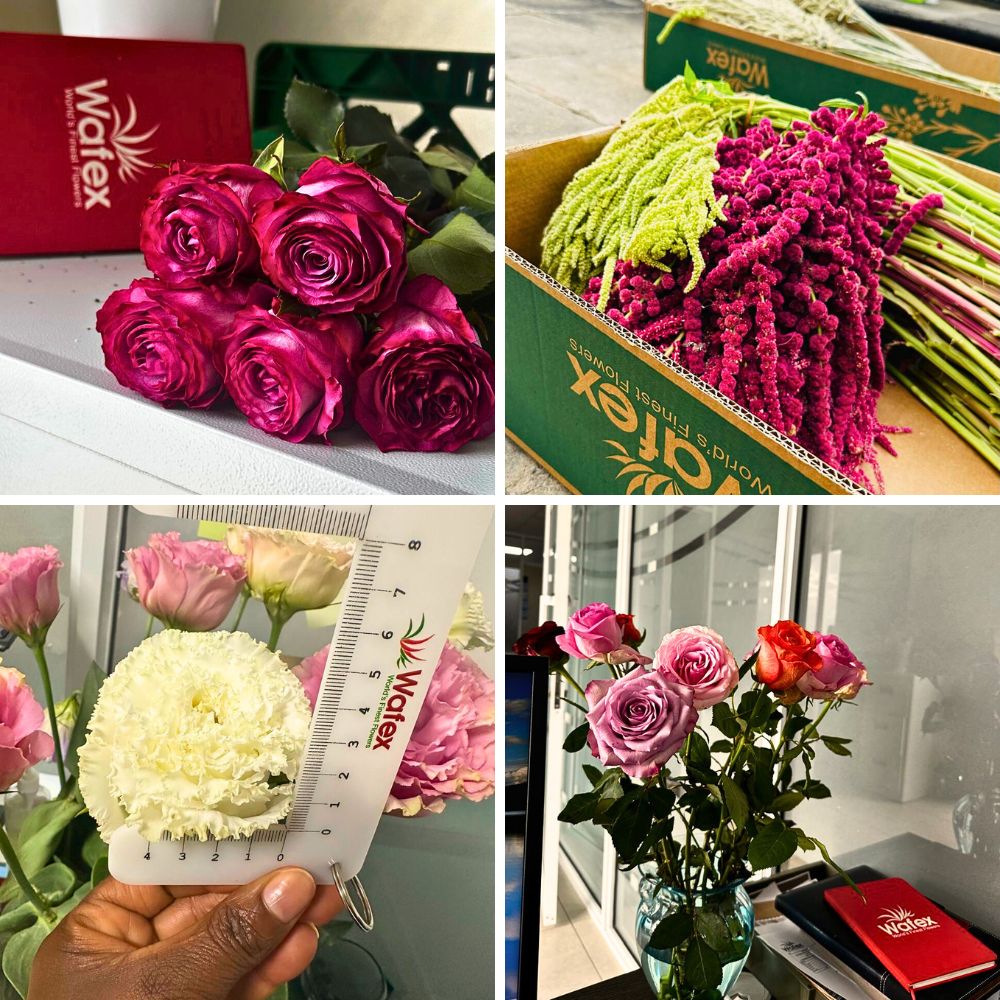
The Quality Assurance Journey Begins at the Source
The ideal climatic conditions in the East African region significantly enhance flower quality and quantity, enabling Wafex Kenya to ensure a year-round supply of exquisite blooms to meet the ever-changing demands of international markets. The consistent sunshine, moderate temperatures, and high altitudes of many areas create perfect conditions for growing flowers with rich colors, strong stems, and exceptional vase life, meaning that whichever flower one needs, Wafex Kenya will deliver it.
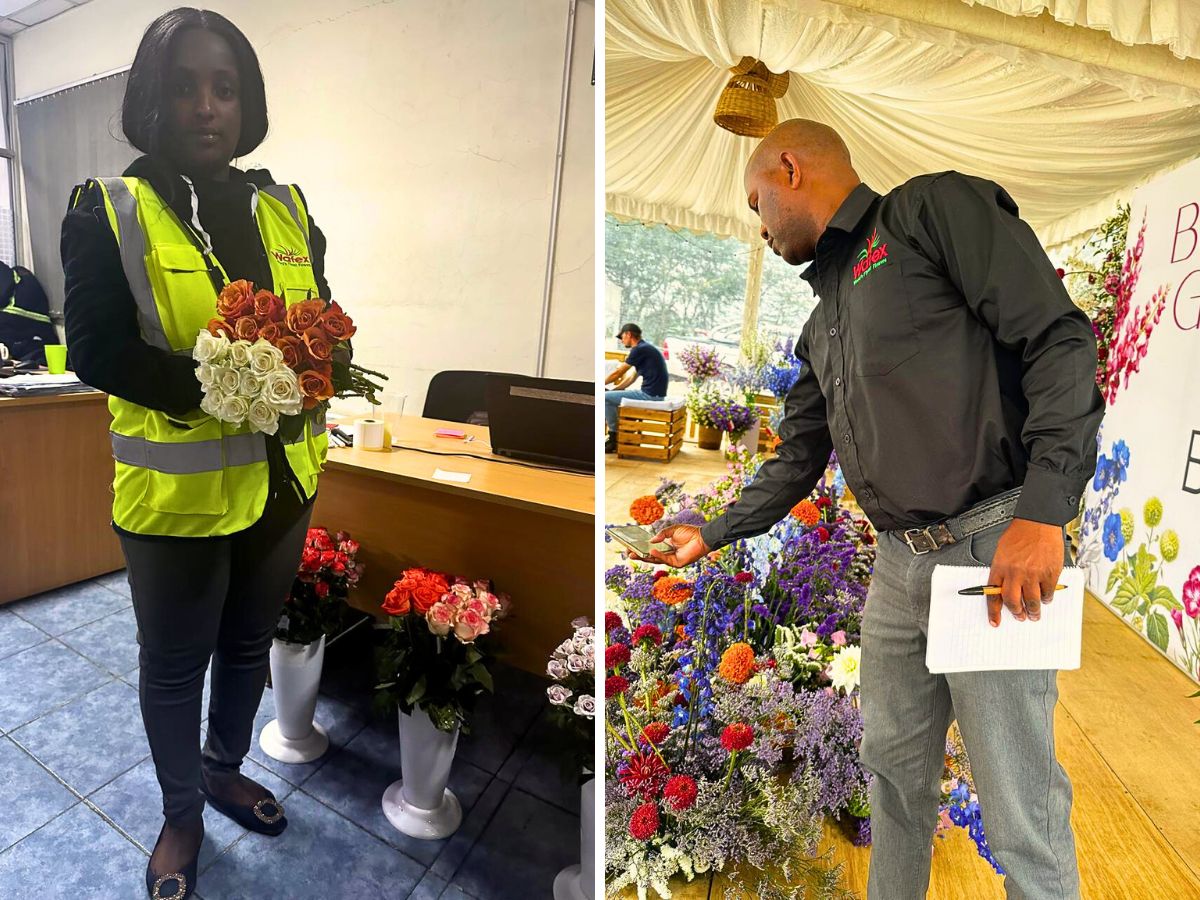
For this flower sourcing company, however, quality assurance begins even before the flowers are harvested. The comprehensive approach, which started with the careful selection of grower partners across the region who share a commitment to delivering the finest flowers to customers, often sees Elijah and his team, conducting regular visits to their partner farms throughout Kenya, Ethiopia, and Tanzania, evaluating growing conditions, cultivation practices, and environmental controls that influence flower quality. John 'JJ' Odhiambo, a key player of this team, has risen fast within the ranks, starting as a security staff member, to become one of the most important members of the quality control team, showing Wafex Kenya's commitment to employee diversity.
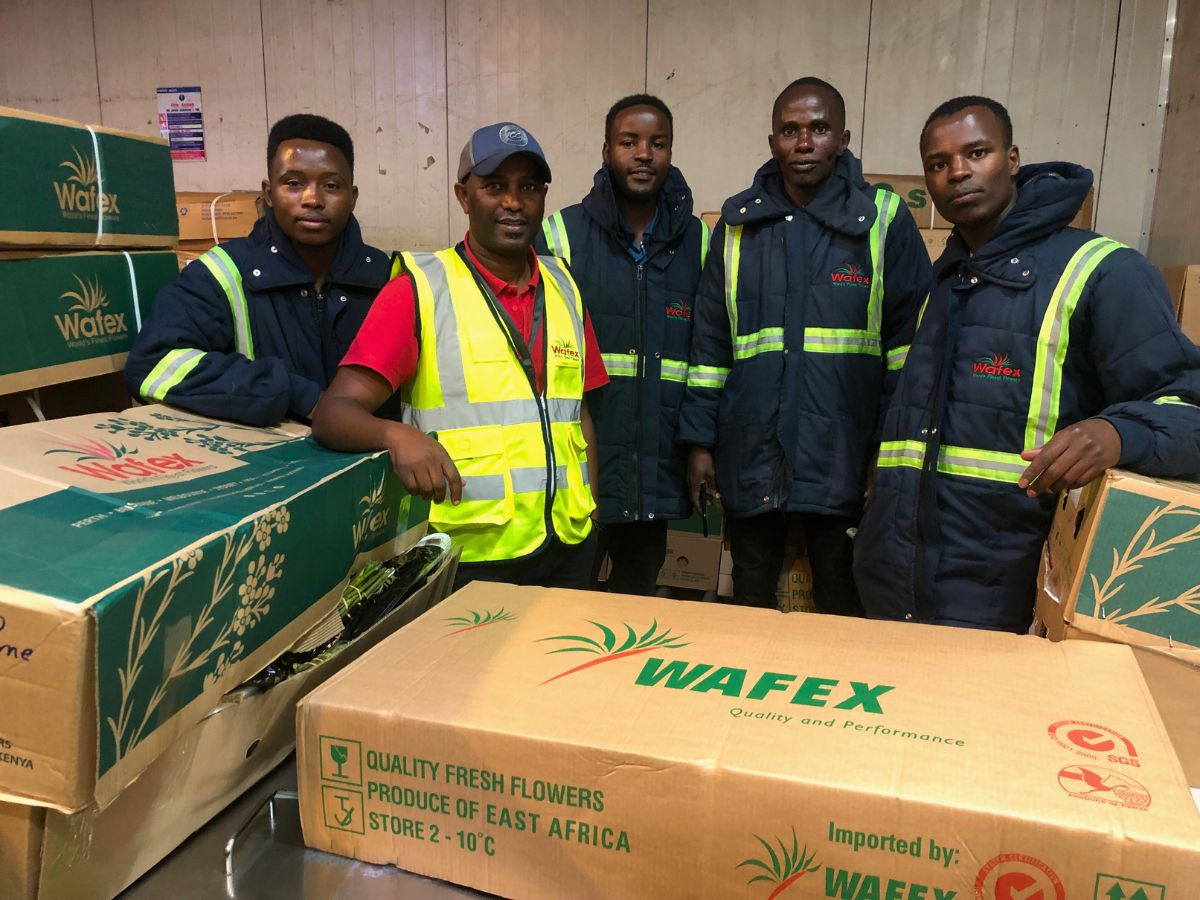
Furthermore, the company has established rigorous standards that all supplier farms must meet, including considerations for pest management practices and cultivation techniques. These partnerships are built on mutual trust and a shared vision of delivering exceptional flowers to the market. Consequently, the growers are required to adhere to these strict horticultural practices, including integrated pest management and disease control protocols, ensuring their flowers are cultivated in environments free from harmful chemicals and pathogens. Elijah, a trained agronomist, often assists the growers, advising them on the best methods to tackle the threats posed by pests and diseases.
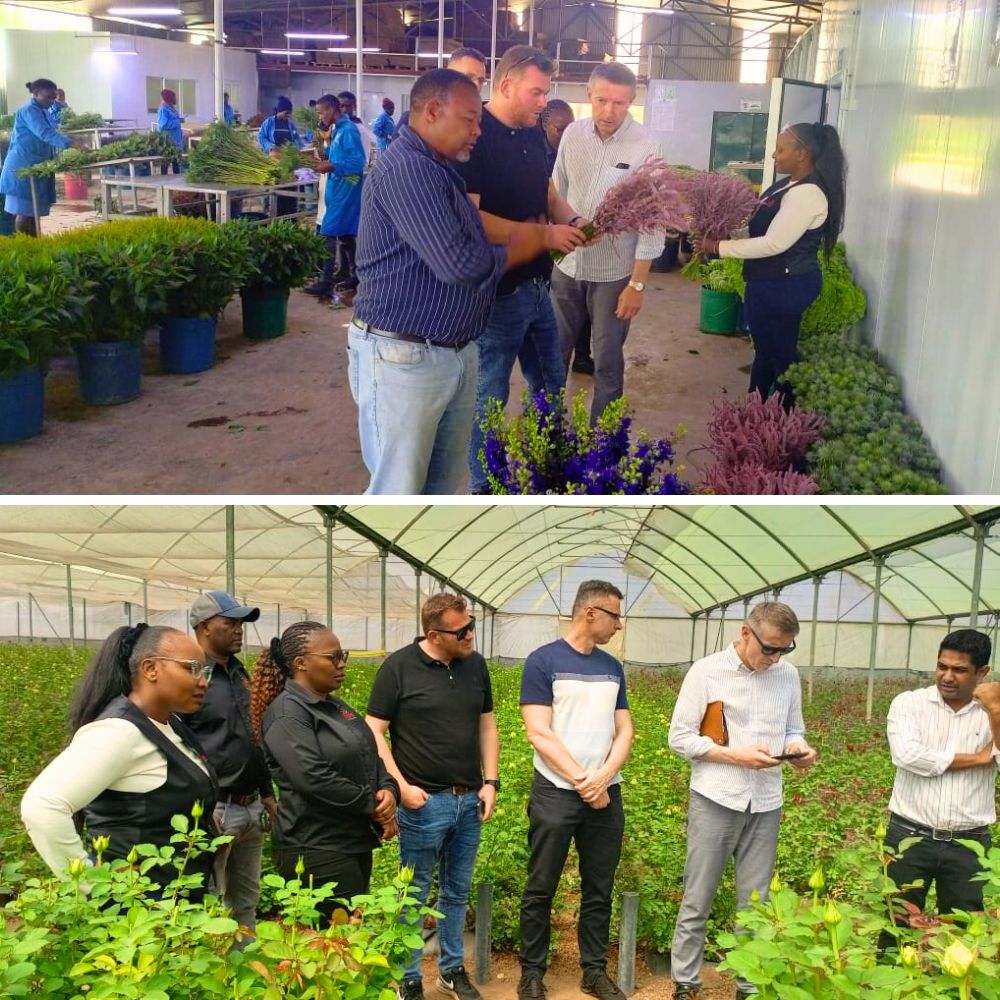
Comprehensive Quality Inspection Protocols
Once flowers are ready for harvest, the quality assurance process intensifies. Wafex Kenya employs a multi-stage inspection system designed to identify and eliminate any flowers that do not meet their exacting standards. This begins in the field, where the grower evaluates samples of flower orders for any signs of pest infestation or disease. Early detection allows for targeted interventions that ensure only healthy flowers enter the supply chain.
After harvest and delivery at Wafex Kenya, each batch undergoes a thorough examination in controlled environments where conditions are optimized to maintain flower freshness and identify even subtle quality issues. The Wafex Kenya team carefully assesses key parameters, including overall flower condition, and any flowers showing signs of infestation, damage, discoloration, or irregularities are immediately removed. The responsible grower is promptly informed so they can deliver better quality replacement flowers.
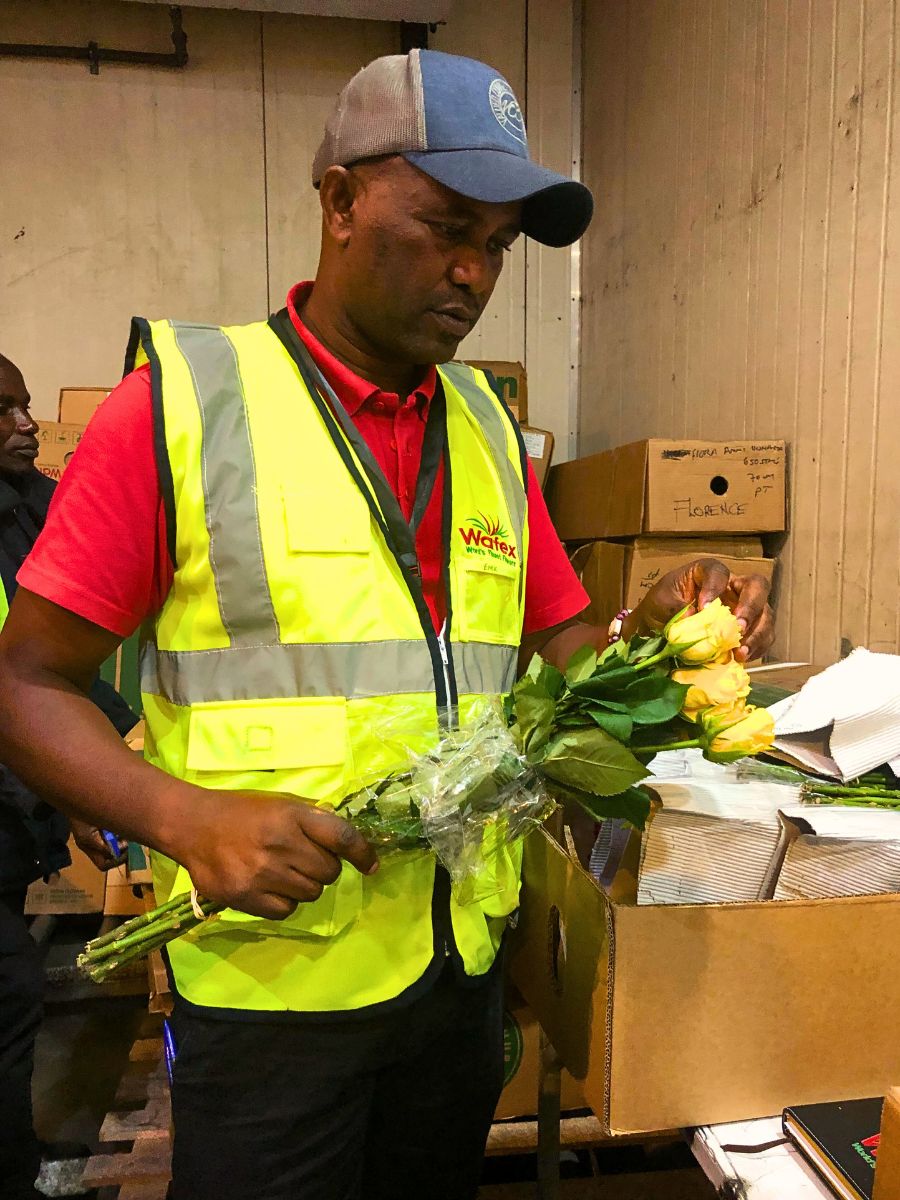
Given the stringent regulations in different markets, pest and disease control represent a critical component of the quality assurance process. Flowers are carefully examined for common pests like thrips, aphids, and spider mites that can damage them or pose quarantine risks for international shipments. Similarly, diseases such as botrytis (gray mold), powdery mildew, or rust are vigorously screened for, as these can quickly spread throughout a shipment and devastate entire consignments.
Furthermore, random samples undergo detailed examination to ensure the highest levels of biosecurity compliance. Plus, the flower sourcing and delivery company also vases flowers, and offers vase life testing for their growers.
Claris Wanjohi:
"They send us the floral products and we test them and send them feed back which gives them an idea of where to improve or which varieties need addressing. We have a controlled vaselife room, which enables us to partner with our growers. We also partner with farms to send new varieties to our clients to test how they handle travel, and give back the feedback."
All these rigorous protocols ensure that every flower leaving their facility meets not only aesthetic standards but also the strict phytosanitary requirements of importing countries, preventing any potential introduction of pests or diseases to new regions.
Mastering Logistics - Speed, Precision, Innovative Packaging, and Cold Chain Integrity
Even the finest flowers can falter without seamless logistics. Wafex Kenya’s partnership with logistics companies like Kuehne + Nagel, a global leader in the trade, ensures flowers move swiftly from their facility to the respective destinations. The cold chain is well managed, with refrigerated trucks and temperature-controlled storage maintaining optimal conditions from the flower farm to Nairobi’s Jomo Kenyatta International Airport (JKIA), then to European hubs.
Additionally, to tackle airfreight challenges, Wafex Kenya optimizes palletization and other strategies, particularly through the use of smart packaging and standardized boxes, which stack uniformly to maximize space and minimize handling issues. The flower sourcing company has, for instance, partnered with Cargolite, a provider of innovative cartons and pallets for the airfreight of cut flowers and herbs, which helps them implement state-of-the-art packaging solutions.
Innovation in Packaging - The Cargolite Advantage
The Cargolite concept is based on several key principles, including reducing carton weight, increasing the pack rates, saving on packaging materials and airfreight, improving the quality, reducing the handling, assuring air pallet uniformity, and reducing the carbon footprint. During a recent visit to grower Zee Flora, one of Wafex Kenya’s partner farms, Martin Kabaka, the Kenya representative for Cargolite, introduced the grower to an innovative packaging box concept that preserves the freshness of flowers and maintains their quality, while containing more flowers per volume and providing superior protection during transit.
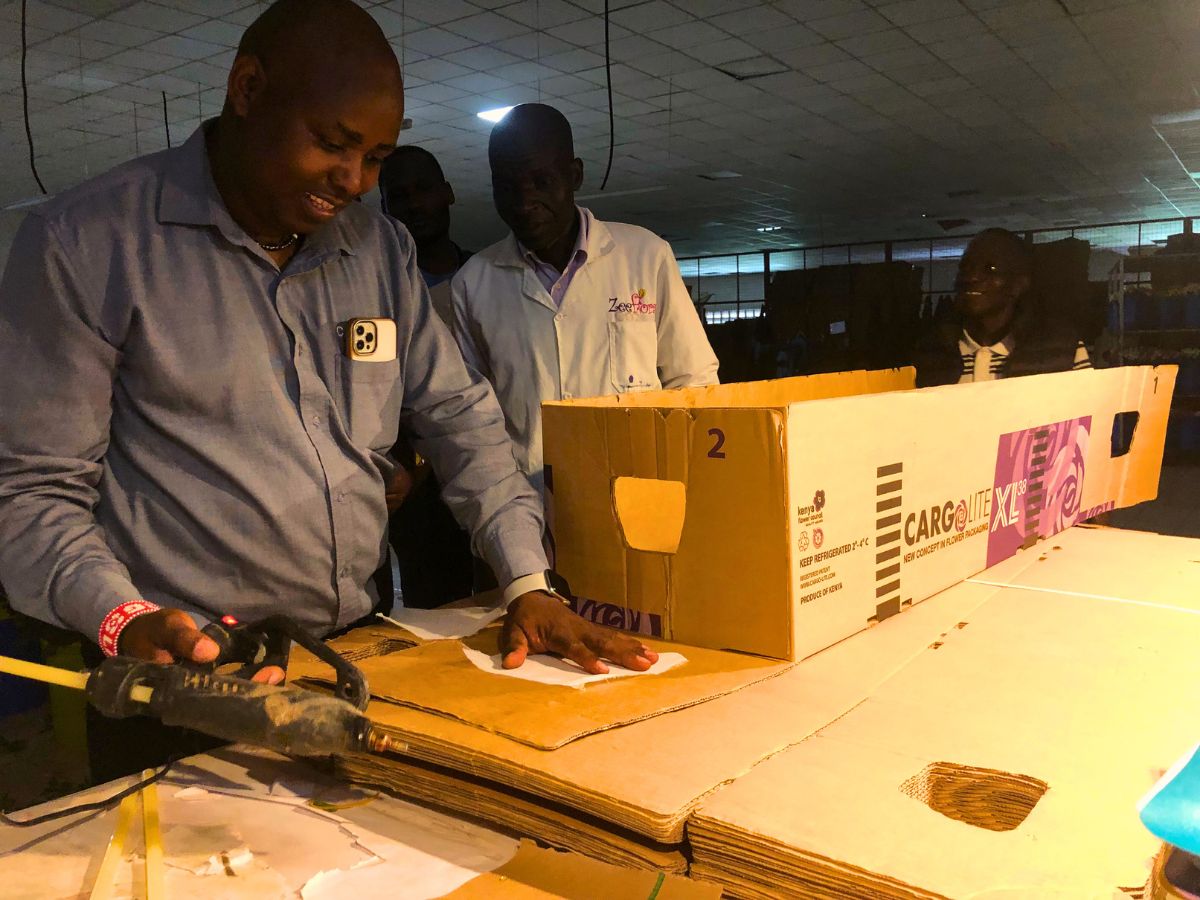
The ingenious design, whose efficacy Elijah was assessing as part of his job description and responsibilities, spreads the weight of the flowers away from the carton's walls, supporting each carton separately and preventing compression damage that often occurs with traditional packaging. The design also maintains the cartons in a level position throughout handling operations, which prevents flowers from shifting or sliding inside the package.
These Cargolite cartons, engineered with internal cardboard frames that withstand significant forces, eliminate the need for bulky protective materials like Single Faced Kraft (SFK) laminates. This increases pack rate, allowing more stems per box without compromising airflow, which is critical for maintaining freshness. For all these efforts, the results always speak for themselves. Because flowers sourced and delivered fresh and in perfect condition by Wafex Kenya grace different supermarkets, florist shops, retail stores, and events worldwide.
Meet Wafex at IFTEX 2025
Wafex will be exhibiting at the IFTEX. Find them at booth C2.09, where they will be showcasing the finest flowers from the Kenyan market. They will be expecting you, so reach out to book an appointment to experience their services and flowers.